In the aftermath of one of deadliest fire hazards of recent times in London, apprehensions about a potential disaster of similar magnitude looms large in the minds of millions of people in Australia. According to latest reports, the number of casualties in the tragic incident at the twenty four storied Grenfell Tower has touched almost eighty. It is understood that this calamity was triggered by the use of non-compliant cladding materials in the building.
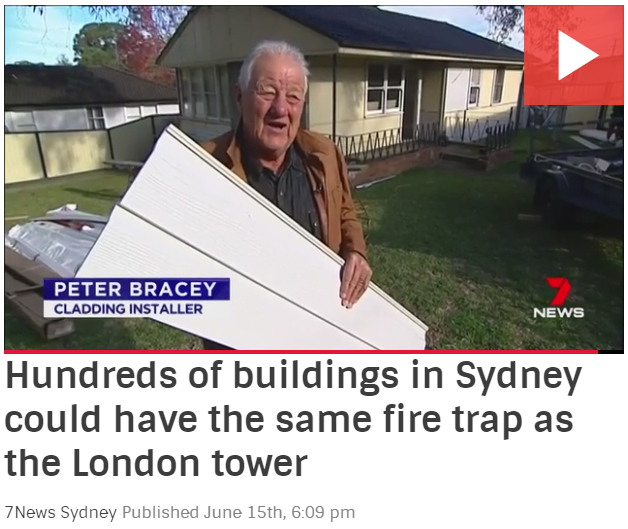
Peter Bracey, a premier cladding installer in Sydney offers only 100% Australian made Palliside cladding that offers a nil combustion ratio.
A number of experts are now suggesting that the recent addition of new aluminium cladding at Grenfell Tower played a significant role behind the fire. Instead of using fireproof insulation, the space between the building structure and the aluminium façade was stuffed with inexpensive and non-fireproof insulation. Some reports claim that the fire was created by an exploding electrical appliance, and was expedited by cladding with inadequate installation and flammable insulation.
The incident at Grenfell Tower is no less than a wake up call for the regulatory authorities in Australia. It is extremely frightful to know that thousands of high-rise buildings in Sydney have used exactly the same cladding materials that were responsible for the fire at Grenfell Tower.
Australia has had its own share of fire disasters over the years. In 2014, Melbourne’s Lacrosse Residential Apartment Building suffered extensive damage from fire caused by a cigarette. The building’s combustible external cladding helped the fire spread quickly to all its floors. Further investigations revealed that this imported cladding material was highly inflammable, and was not tested to Australian standards.
Unfortunately, the regulatory bodies in Australia have not responded adequately to the incident at the Lacrosse Residential Apartment. Even today, the nature of cladding used in thousands of apartment complexes in Sydney is exactly similar to the one that accelerated the fire in Grenfell Tower. A very high percentage of these buildings have an inflammable cladding done, using aluminium composite panels with a polyethylene core. Experts suggest that replacement of the existing cladding in these buildings is not a viable solution because the cost may touch billions of dollars.
Along with the increase in the number of high-rise buildings throughout the country, the application of flammable cladding materials have also become common over the last decade or so. Some of the most common benefits of cladding are enhanced rigidity, insulation, and cosmetic improvements of the building. However, most of the cheap and imported cladding materials comprise of plastic cores compressed between two aluminium panels, and are less fire retardant compared to the compliant materials.
The best step towards protecting our buildings from potential fire hazards is to use non flammable cladding materials that are tested to perform under the extreme Australian climate. The desirable attributes of a safe cladding material has been clearly specified in the Australian fire standard (AS1530.3). The use of non-combustible building materials has also been recommended by the National Construction Code (NCC). In order to comply with the Australian fire standard (AS1530.3), the cladding materials are required to have the following qualities
- Zero ignitability
- Zero heat evolved
- Zero spread of flame
- Smoke developed 8
As per recommendations from the fire safety experts all over the country, the best cladding option for the Australian buildings is solid UPVC Palliside Cladding. Australian manufactured and engineered to tolerate the hostile Australian climate, this material is used extensively in areas that are bushfire prone. Palliside is also capable of handling extreme temperatures with a temperature range of -10°C to 60°C as well as many other benefits.
Please feel free to contact us to find out more about ensuring unbreachable fire safety for your family and household by installing the best quality Palliside cladding.